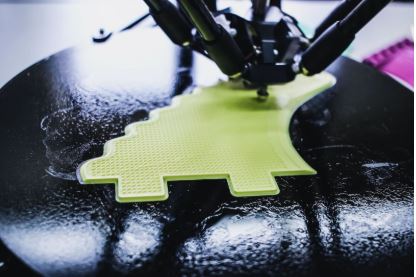
If you’re into 3D printing, you’ve likely faced the challenge of choosing the right material. Your choice directly affects the durability, weather resistance, and ease of printing. Among the many options available, PETG, ABS, and ASA are three of the most popular, each offering unique advantages. PETG is easy to print and strong, ABS withstands high temperatures, and ASA is highly resistant to sunlight and harsh weather conditions. This article will compare all three and help you determine the best project.
Why is PETG So Popular?
PETG is highly durable and impact-resistant, making it ideal for functional parts. For example, if you need to print a bike mount or an electronics enclosure, PETG ensures longevity without breaking under minor stress. PETG is resistant to many chemicals, oils, and even mild acids, unlike ABS. This makes it an excellent option for technical parts that might come into contact with aggressive substances, such as liquid storage containers or protective casings for tools. You can find more insights into 3D printing materials, techniques, and best practices by checking out Sketchat!
One of the main reasons PETG has become so popular is its stability during printing. PETG has minimal warping and adheres well to the print bed, even on open-frame printers. If you’re just starting with 3D printing, PETG can help you avoid many common printing issues.
PETG comes in opaque and transparent varieties, making it an excellent choice for decorative elements, light fixtures, or custom electronic cases. If you need strong yet stylish parts, PETG is a fantastic option.
Of course, PETG isn’t perfect in every scenario.
PETG softens when exposed to high temperatures for extended periods. If you need a material for parts subjected to extreme heat (such as near a car engine), ABS or ASA would be a better choice. Additionally, PETG is less UV-resistant than ASA, which can become brittle and lose transparency when exposed to direct sunlight for long periods.
PETG produces delicate strings during printing due to its high viscosity. However, this issue can be minimized with proper retraction and temperature settings.
ABS
Imagine you’re designing a part for your car — a custom phone holder for the dashboard. It must withstand high temperatures on a hot summer day, be durable enough to handle vibrations, and not deform over time. This is where ABS shines.
What Is ABS?
ABS is a rigid, impact-resistant material often used in industrial applications. It’s the same plastic found in LEGO bricks — durable, slightly flexible, and able to take a beating. Whether you’re printing mechanical parts, protective casings, or enclosures for electronics, ABS provides a strong and long-lasting solution.
✅ Resistant to Heat (Up to 100°C)
Unlike PETG, which can soften at moderate temperatures, ABS remains stable even in high-heat environments. That’s why it’s commonly used in automotive and industrial settings. ABS is a solid choice if you need a part that won’t deform when left in a hot car or near a heating element.
✅ Ideal for Post-Processing
ABS is one of the best materials for finishing touches. You can sand it to smooth out imperfections, paint it for a professional look, or use acetone vapor smoothing to achieve a glossy, injection-molded finish. ABS is a favorite for those who want a refined, polished result.
Challenges of ABS
One of the biggest struggles with ABS is warping — when the edges of your print curl up due to uneven cooling. Your perfectly designed part might look like a warped potato chip without proper settings or an enclosed printer. A heated bed and an enclosed chamber help minimize this issue by maintaining a stable temperature.
Because ABS contracts as it cools, sudden temperature drops can cause layer separation. Printing it in an enclosed, temperature-controlled environment is highly recommended. If your workspace is cold or drafty, ABS might give you trouble.
ABS produces noticeable fumes when printed, which contain small amounts of potentially harmful particles. Proper ventilation is crucial — either print in a well-ventilated area or use an enclosure with an air filtration system.
ASA
Let’s say you’re printing a custom garden hose holder or a sign for your business that will be exposed to the sun, wind, and rain. ABS might hold up for a while, but eventually, UV rays will cause it to fade and become brittle. This is where ASA comes in.
Why Choose ASA?
ASA is designed to withstand outdoor conditions, making it perfect for anything that must endure harsh weather — signage, outdoor fixtures, or car parts exposed to direct sunlight. ASA maintains the durability of ABS while offering better resistance to environmental factors. If you need a material that’s both tough and long-lasting outdoors, ASA is the way to go.
Although ASA still benefits from an enclosed printer, it’s generally easier to work with than ABS regarding warping. This makes it a more reliable choice if you need high strength without the hassle of extreme print failures.
Challenges of ASA
1. ASA’s advanced properties come at a cost — it’s pricier than both ABS and PETG. If your project doesn’t specifically require UV resistance, you might opt for ABS to save on material expenses.
2. While it’s less prone to warping than ABS, ASA still contracts as it cools. An enclosed, temperature-controlled environment is the best way to ensure high-quality prints.
Which Material Should You Choose?
🔹 For general-purpose and easy printing → PETG
Perfect for beginners and functional parts that don’t require high heat or UV resistance.
🔹 For high-heat applications and strength → ABS
Great for mechanical parts, automotive components, and post-processing projects.
🔹 For outdoor and UV-resistant prints → ASA
Ideal for long-lasting outdoor applications and parts exposed to extreme weather.
Each material has strengths – the best choice depends on your specific needs. Whether you’re designing functional parts, artistic models, or industrial components, understanding the properties of PETG, ABS, and ASA will help you make an informed decision.