The production of plastics has grown exponentially in the past decade. Stats suggest that nearly 400 million tonnes of plastics is produced every year around the world. Moreover, with the evolution of technology, plastic manufacturers have developed various methods to produce high-quality plastics. However, injection moulding is still one of the most favoured means of plastic production. More than 3o% of plastic products around the world are produced through injection moulding.
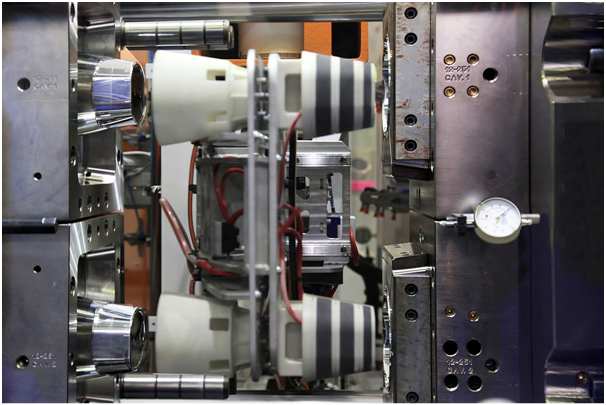
What Is Injection Moulding?
Injection moulding is a production process where products are produced by injecting molten materials in a mould. It is an extremely efficient manufacturing process to produce plastic parts in large volume; in terms of thousands or even millions. It is the most preferably used for mass-production methods where the creation of identical products is required.
How Does Plastic Injection Moulding Process Work?
During injection moulding, the melted plastic is injected into a mould under high pressure with the help of an injection moulding machine. In the mould, the material is left to cool and solidify. Afterwards, the material is released by opening the mould in two halves. With this technique, a pre-determined and fixed form of the plastic product is obtained.
Major Problems during Injection Moulding of Plastics
The process of injection moulding requires high-expertise and attention to every tiny detail. Even minor errors can cause substantial losses to the manufacturers. The defects can be high brittleness, the formation of bubbles on the surface, cracking and splay.
Now the big question arises for manufacturers is why all these problems incur in their products?
The first and foremost reason for these defects is excess moisture. During the moulding process, if excessive moisture is present in the air, it can lead to significant defects and also causes mould sweating.
What is Mould Sweating?
Mould sweating is an unwanted by-product that occurs during the injection moulding process. It causes rusting on the machine bed and the mould, which affects the lifetime of the equipment. During the injection moulding process, the plastic melt is kept inside the mould to cool and take the desired shape. Chilled water is used to speed up the cooling process and reduce the time of a process cycle. However, while the chilled water cools the mould, the moisture present in the surroundings condenses and results in the formation of water droplets on the surface of the mould, which is known as mould sweating.
How to Prevent Severe Effects Of Moisture during Injection Moulding?
The best solution to prevent moisture from affecting the quality of the products is by using mould dehumidification systems. These systems prevent the drastic effects of moisture by absorbing humidity and supplying dry air during the time of production. By using mould dehumidification systems, manufacturers can ensure that the mould does not deteriorate due to excess condensation.
Working of Mould Dehumidification Systems
The moisture-laden air enters the dehumidification system via a process inlet and passes through a desiccant wheel which absorbs the moisture. The wheel absorbs moisture through the continuous physical adsorption process. Once moisture is removed from the air, it is transferred to the conditioned area via the process outlet. The rotating desiccant wheel moves in the reactivation segment before saturation, when the moisture is driven off with the help of hot air blowing through the reactivation segment. The rotor with its continuous movement provides effective dew point control and stable temperature.
Advantages of Mould Dehumidification Systems
- Prevents mould sweating; thus, enhancing the lifetime of equipment and quality of products
- Due to the effective working of machines, the production cycle time improves effectively
- Mould dehumidification systems can provide dry air to multiple machines at a time increasing the production
- Reduces scrap rate
In a nutshell, one can say that using mould dehumidification systems can not only standardise the air quality during injection moulding but also increase the production efficiency in the manufacturing plant. As the demand for plastic products is growing at an alarming rate, it is vital that manufacturers install these systems in their plants to stay in sync with the demand and supply.